Global economy 2023: COVID-19 turned global supply chains upside down – 3 ways the pandemic forced companies to rethink and transform how they source their products
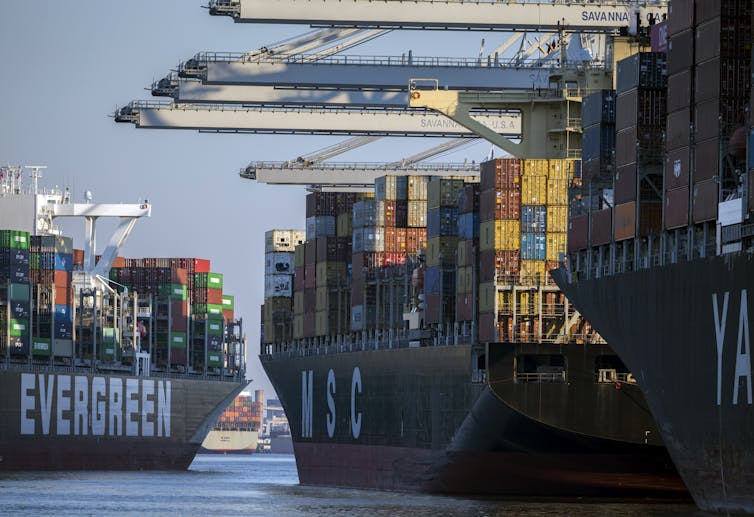
By Nada R. Sanders, Northeastern University
This is the sixth and final installment in our series on where the global economy is heading in 2023. It follows recent articles on industrial action, inflation, energy, food and the cost of living.
The global supply chains that modern companies depend on were turned upside down three years ago after COVID-19 emerged in China. The spread of the new respiratory illness and efforts to slow it resulted in shortages of everything from toilet paper and prescription drugs to refrigerators and semiconductors. Even today, retailers continue to struggle to keep some products, including household items like Tylenol and eggs, in stock. Overall stress in supply chains remains high.
Because shortages, delays and bottlenecks can hurt their bottom line, many companies that didn’t go bust during the pandemic have been rethinking their supply chains and implementing changes to make them more resilient.
As a supply chain expert, I have observed three major shifts in how companies manage their supply chains – changes that will significantly affect consumers and businesses alike.
1. Bringing supply chains home
One of the main downsides of having supply chains that span the globe is that they are more vulnerable to problems outside of a company’s control, such as an earthquake that strikes a key supplier or a citywide lockdown that shuts down factories.
That’s why companies in every industry have been working to relocate suppliers and production facilities closer to home or geographically spreading them out so that they’re not so dependent on one country or region. The goal is to ensure they can withstand disruptions and maintain business continuity.
The pace of reshoring – the process of shifting production and manufacturing to domestic locations from overseas factories – has surged in recent years. Over 60% of European and U.S. manufacturing companies expect to reshore part of their Asia production in the next three years, according to a survey conducted in early 2022.
A more recent survey found that U.S. transport and manufacturing reshored about 350,000 jobs in 2022, up 25% from the previous year.
This trend not only has support from government subsidies but retailers as well. Walmart, one of the world’s biggest retailers, has committed to help its suppliers reshore by increasing its purchases of U.S.-made products by US$350 billion over the next decade. In the U.K., a survey of 750 small businesses found that 2 in 5 are considering switching to domestic manufacturers to avoid COVID-19 disruptions and high shipping costs.
At the same time, other companies are trying to diversify their sources of supply, often away from China, which until recently was regularly locking down whole cities to maintain its now-lapsed zero COVID-19 policy. India and Vietnam are popular destinations.
U.S.-based Apple, for example, frustrated by product delays in China, where 98% of its iPhones are made, recently started producing models in India. In addition, Foxconn, its largest supplier, agreed to expand production in Vietnam. Overall, U.S. manufacturing orders from China are down 21% since August 2022.
In Europe, carmaker Volvo announced in July plans to open its first European factory in 60 years in Slovakia. And leaders of the U.S., Mexico and Canada are meeting to discuss ways to encourage more investment in the region, which may result in more reshoring.
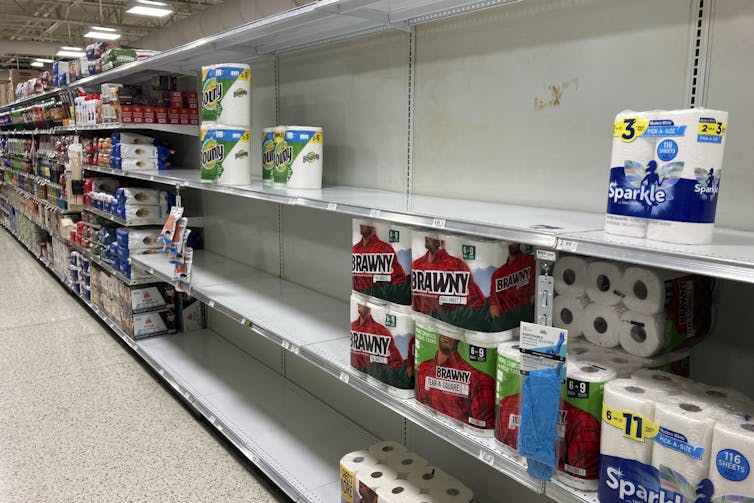
2. Investing in more technology
One of the biggest issues when the COVID-19 pandemic began was that companies often didn’t know what was going on with their suppliers because of poor technology. For example, prior to the pandemic, over 50% of companies didn’t communicate with or know the locations of all their suppliers, making it difficult to anticipate shortages.
Companies have since learned, if they didn’t already know, that being able to see what is happening along their supply chains is critical to avoiding and adapting to disruptions. And modern digital technologies are key to making this happen.
This includes everything from state-of-the-art software to better communicate with suppliers to cloud computing for efficient data storage, artificial intelligence tools to make better decisions and robotics for automating processes. Implementing these new technologies is the biggest global corporate priority for 2022, according to strategic consultancy the Hackett Group.
3. From ‘just-in-time’ to ‘just-in-case’
One of the great supply chain advancements in recent decades is a Japanese management philosophy known as “just-in-time.”
While the essence of the philosophy is eliminating waste, businesses reduced just-in-time to the idea of having low or even zero inventory. That meant carrying as little stuff in warehouses as possible to minimize storage costs, maximize efficiencies and yield higher profits. As long as there were no disruptions, the system worked.
However, just-in-time made businesses vulnerable to even small disruptions. Companies’ super-lean supply chains meant the disruptions caused by the pandemic – and pretty much anything else – were amplified considerably, making even a hiccup potentially cascade into a major problem.
Companies now fearful of shortages are moving toward carrying more inventory. Since the pandemic began, many have been shifting from just-in-time to a “just in case” model. While having more inventory will make it less likely companies will experience shortages, it’s also more costly because it can lead to a lot of excess stock and products becoming obsolete before they’re sold.
But this trend, like the others, is unlikely to change anytime soon despite the elevated costs they’ll incur. That is, companies learned that the cost of empty shelves was higher than the cost of some inefficiency. In most cases, these costs will be passed on to consumers in terms of higher prices – which may be bad news for consumers tired of inflation.
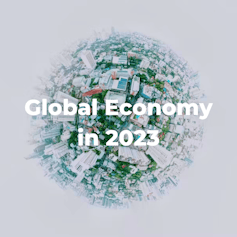
This article is part of Global Economy 2023, our series about the challenges facing the world in the year ahead. You might also like our Global Economy Newsletter, which you can subscribe to here.
Nada R. Sanders, Distinguished Professor of Supply Chain Management, Northeastern University
This article is republished from The Conversation under a Creative Commons license. Read the original article.